Predictive Maintenance
IoT Connectivity for Predictive Maintenance: Solutions and Benefits
/Industry/industry-predictive-maintenance.jpg?height=600&name=industry-predictive-maintenance.jpg)
How you can simply connect Predictive Maintenance?
A small SIM card and a smart plattform provides everything you need.
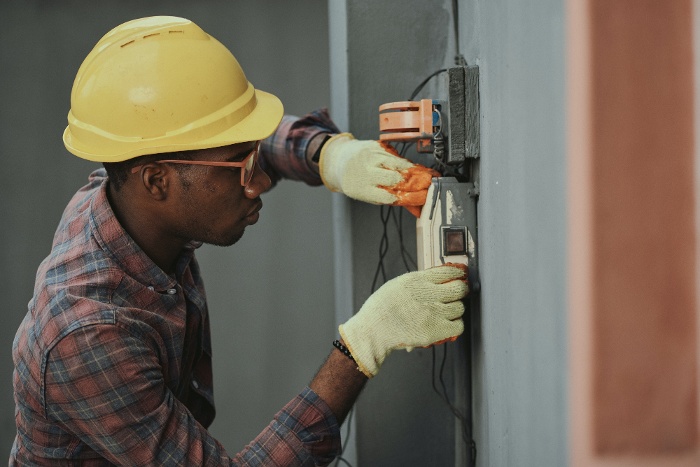
By some estimates, unscheduled downtime costs manufacturers $50 billion every year. While preventive maintenance plans significantly decrease this unplanned downtime, they can’t prevent every breakdown, and often result in wasted parts and services.
Predictive maintenance leverages the Internet of Things (IoT) to close this gap by collecting real-time data and detecting abnormal performance. Connected sensors analyze: vibrations, temperature, acoustics, speed, and other factors, analyzing it against historical failure patterns and optimum performance levels. This ensures manufacturers can catch early warning signs to predict and prevent breakdowns. For Original Equipment Manufacturers (OEMs) and system integrators, equipping machinery with connected sensors is key to reducing downtime, decreasing operating costs, creating safer workplaces, and extending the life of critical assets.
Here’s how IoT predictive maintenance is changing various industries today, and how emnify can help you add connectivity to your equipment.
Predictive maintenance applications
Manufacturing processes
Agricultural equipment
Smart buildings
Oil and gas
Our Customers trust us...
Benefits of predictive maintenance
-
Adding IoT connectivity and predictive maintenance capabilities to equipment provides several valuable benefits for OEMs and their customers. First and foremost, it reduces downtime - even if there’s already a preventive maintenance plan in place. But predictive maintenance also increases the lifespan of equipment, improves workplace safety, and lowers maintenance costs.
Specifications:
Preventive maintenance plans operate on a fixed schedule. If equipment needs maintenance sooner (usually due to abnormal usage), a preventive maintenance plan won’t account for that, which can lead to breakdowns. Additionally, purely relying on preventive maintenance can result in unnecessary scheduled downtime when parts and equipment don’t need service.
Predictive maintenance doesn’t follow a schedule, so it helps prevent breakdowns that would otherwise occur between services. When equipment that doesn’t need to follow a fixed maintenance schedule to stay in compliance or under warranty, predictive maintenance can also reduce scheduled downtime by empowering manufacturers to avoid unnecessary maintenance.
-
Adding IoT connectivity and predictive maintenance capabilities to equipment provides several valuable benefits for OEMs and their customers. First and foremost, it reduces downtime - even if there’s already a preventive maintenance plan in place. But predictive maintenance also increases the lifespan of equipment, improves workplace safety, and lowers maintenance costs.
Specifications:
Every time a piece of equipment breaks down or a component fails, it has the potential to cause greater damage. Operating equipment to the point of failure also increases the wear on other components and systems, even if they don’t break.Predictive maintenance extends the life of assets by ensuring they don’t reach these breaking points, and managers are always aware of unusual performance.
-
Adding IoT connectivity and predictive maintenance capabilities to equipment provides several valuable benefits for OEMs and their customers. First and foremost, it reduces downtime - even if there’s already a preventive maintenance plan in place. But predictive maintenance also increases the lifespan of equipment, improves workplace safety, and lowers maintenance costs.
Specifications:
You never want employees operating heavy machinery when it fails. In some work environments, breakdowns can easily cause injury or death, either because the equipment directly causes harm, or because it doesn’t work when someone depends on it.Predictive maintenance alerts equipment operators when something isn’t behaving as usual, and it gives manufacturers time to schedule maintenance before minor issues lead to dangerous breakdowns.
-
Adding IoT connectivity and predictive maintenance capabilities to equipment provides several valuable benefits for OEMs and their customers. First and foremost, it reduces downtime - even if there’s already a preventive maintenance plan in place. But predictive maintenance also increases the lifespan of equipment, improves workplace safety, and lowers maintenance costs.
Specifications:
When technicians aren’t trying to coordinate emergency repairs in the middle of your operations, they need less time to resolve maintenance problems. In general, reactive maintenance is more costly than proactive maintenance, and implementing predictive maintenance reduces the likelihood that your equipment will need major work done.