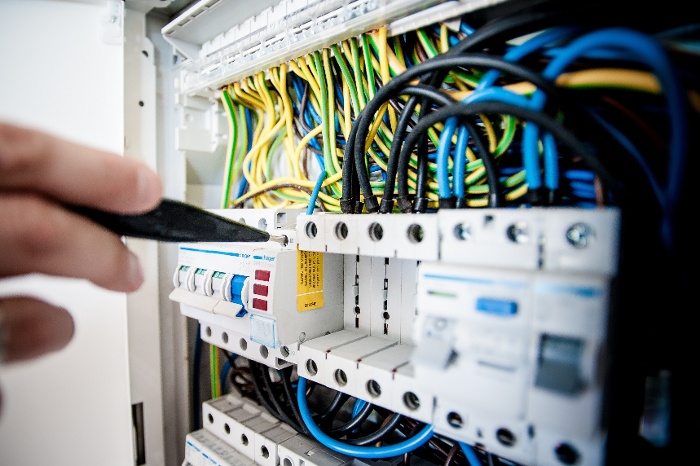
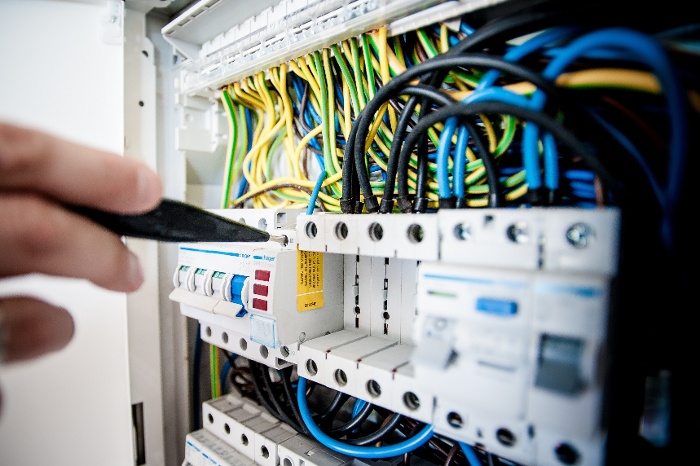
Predictive maintenance is a maintenance approach that uses connected sensors to measure a piece of equipment’s performance and schedule service or repairs when performance falls below a predetermined threshold. This reduces both scheduled and unscheduled downtime, minimizes waste, and keeps equipment operating at its best.
Unscheduled downtime comes at a staggering cost. Some estimates suggest it costs manufacturers $50 billion per year. And 82 percent of manufacturers say it’s happened to them in the last three years.
Predictive maintenance eliminates these costs and more.
While predictive maintenance is immensely valuable and widely applicable, it’s not the norm in many industries. Numerous businesses that would benefit from predictive maintenance have yet to implement preventive maintenance—a half-measure that reduces unscheduled downtime but results in excess expenses and scheduled downtime. Strangely, you’ll often hear preventative maintenance hailed as the gold standard of maintenance approaches. But prediction is more efficient than prevention, and if you’re only using preventive maintenance, you’re missing a valuable opportunity to reduce costs and minimize the disruption to operations.
In this article, we’ll explain why predictive maintenance is the most effective approach, how predictive maintenance works, the benefits it provides to industrial operations, and how cellular IoT addresses many challenges with implementation. Here is a summary of what we will be covering:
- Reactive maintenance vs. preventive maintenance vs. predictive maintenance
- How does predictive maintenance work?
- Benefits of predictive maintenance
- How cellular IoT is revolutionizing predictive maintenance
- Connect your predictive maintenance solution with EMnify
Let’s start by taking a closer look at the types of maintenance in use today.
1) Reactive maintenance vs. preventive maintenance vs. predictive maintenance
Whether a business is in agriculture, manufacturing, power production, construction, transportation, or retail, there are three main approaches to maintenance: reactive maintenance, preventive maintenance, and predictive maintenance.
Each type of maintenance has a very different impact on downtime, expenses, equipment lifespan, safety, and overall disruption to operations. In practice, the difference comes down to when and how the business decides a piece of equipment needs servicing.
Usually, these maintenance practices aren’t independent. Preventative maintenance is designed to reduce reliance on reactive maintenance, and predictive maintenance takes this further.
1.1) Reactive maintenance
Reactive maintenance follows the adage, “If it ain’t broke, don’t fix it.” This is often the default approach to maintenance because it doesn’t require any planning or forethought, but it’s also the most disruptive and expensive type of maintenance. And unfortunately, even with a preventive maintenance plan, manufacturers will have occasional reactive maintenance work when equipment breaks down from misuse, abnormal usage, or other unforeseen circumstances.
Reactive maintenance leaves manufacturers scrambling to work around unscheduled downtime, and without a maintenance plan, they’re stuck buying new equipment sooner and more often. When a component fails, it can cause more significant damage as well, so instead of replacing a single part, a business may be stuck repairing several, or replacing the entire piece of equipment.
Breakdowns can (and often will) happen when you least expect them, and when you’re least prepared to deal with repercussions. It doesn’t matter if you’re in the middle of operations, your spare equipment is in use, you don’t have the required parts in stock, or your mechanics are tied up—the maintenance simply has to happen when the failure occurs. In some cases, a business may have to wait days or weeks to even begin repairs.
Depending on the industry and circumstances, reactive maintenance can lead to missed deadlines, lost production, and lost business, damaging your brand reputation and potentially impacting future projects.
1.2) Preventative maintenance
Preventative maintenance is when maintenance happens on a fixed schedule based on estimates of how long parts and equipment should last. This can be informed by a piece of equipment’s work order history, manufacturer recommendations, industry standards, government regulations, or a combination of these guidelines. A preventive maintenance schedule may be based on time since the maintenance was last performed, hours of operation, or other conditions relating to the equipment’s use.
Preventative maintenance is proactive, not reactive, and it dramatically reduces lost time due to unscheduled downtime. Planned repairs will always be less disruptive to operations because you can see them ahead of time and work around them. Additionally, by reducing breakdowns, businesses can avoid more significant damage and the costly repairs that come with it.
Still, there are three downsides to relying on preventive maintenance:
- It means servicing equipment before it needs to be serviced, which increases downtime. Scheduled or not, the equipment isn’t available for use.
- It means replacing parts that don’t need to be replaced yet. The parts you’re replacing may still have plenty of life left, but following the schedule means replacing them anyway.
- Breakdowns can still occur before equipment is scheduled to be serviced, especially if there has been abnormal usage, improper use, or anomalies.
Implementing a preventative maintenance schedule doesn’t require software, but facility managers and fleet managers will typically use facility management software or fleet maintenance software to help coordinate service, parts, and operations around each asset’s schedule.
Preventive maintenance is a half-measure. It’s far better than relying on reactive maintenance, and it’s often crucial to keep equipment under warranty and in compliance, but it can also result in wasted time and money, and it doesn’t completely eliminate failures. If you don’t know how close your parts and equipment are to actually failing, you can’t maximize their utility and minimize the disruption maintenance causes to operations. That’s where predictive maintenance comes in.
1.3) Predictive maintenance
Predictive maintenance is based on real-time performance, not a predetermined schedule. Businesses apply machine learning algorithms to real-time and historical machine performance data. Using IoT sensors, these algorithms can detect the early warning signs of part failure, including things like vibrations, sounds, temperature, speed, or overall performance. This enables businesses to maximize the utility of their equipment by waiting to schedule repairs or services until they’re truly needed, detecting issues early.
This approach ensures that your assets only have downtime when they absolutely need it, your parts only get replaced when you’ve used them for as long as you safely can, and you won’t be caught off guard by breakdowns.
Since it relies on connectivity, predictive maintenance is most common in industrial IoT applications like smart buildings, smart factories, and smart agriculture.
Predictive maintenance is the true gold standard of the maintenance world. Here’s how it works.
2) How does predictive maintenance work?
You can’t predict equipment failures until you know how something operates in peak condition and the threshold at which it will fail. So predictive maintenance always starts with monitoring your assets in all of the circumstances they regularly operate in. Then, in addition to using a maintenance plan to keep equipment in compliance and under warranty, you can schedule maintenance or an inspection when the asset is no longer operating the way it did in peak condition.
But with past data, you can also push your assets closer to the point of failure without actually causing failure, allowing you to avoid scheduling maintenance you don’t need.
2.1) Recognizing failure patterns
Predictive maintenance works best by using past data to determine an asset’s failure pattern, applying current data to that pattern, and then making predictions. Typically, this relies on machine learning, which enables software to process vast amounts of data to recognize patterns, then make intelligent decisions based on the relationship between your real-time data and historical patterns.
For predictive maintenance to work, you have to know which conditions to watch for. Applying machine learning to your past data illuminates which components have failed and what conditions changed at the time of failure. But even if you’re simply comparing present conditions to your established baseline, you need to isolate the change and where it took place.
2.2) Measuring changes in conditions
IoT sensors can detect various changes in conditions, including increases or decreases in vibrations, temperature, acoustics, speed, production, and more. The conditions that signal failure will dictate which types of sensors you need, and depending on the asset, you may need to install them on multiple components or systems.
More on this topic, check out our article about remote condition monitoring.
2.3) Managing IoT maintenance data
These sensors transmit performance data to a central manufacturing execution system (MES) or SCADA, facility management software, fleet management software, or Computerized Maintenance Management Software (CMMS), which then creates alerts when it’s time to schedule services or repairs.
2.5) Scheduling maintenance service
In some cases, you may know exactly which component has caused a change in conditions, such as an increase in temperature. But often, the change in condition will indicate that it’s time for a technician to inspect the equipment to determine the underlying cause. Either way, effective predictive maintenance requires you to have spare parts and equipment on hand, based on your past data about which components are most likely to fail.
As with preventive maintenance, you’ll also want to have a backup plan in place for every piece of equipment—or else plan your operations around the scheduled downtime—so that you can minimize the disruption to your business.
3) Benefits of predictive maintenance
Predictive maintenance provides several key benefits to businesses with high maintenance needs. Many of these are also benefits of preventive maintenance, but predictive maintenance maximizes them.
3.1) Lower operating costs
The better your assets run, the fewer resources they’ll consume during daily operations and the more production value they’ll yield. Predictive maintenance helps you keep your assets in the best condition for as long as possible, scheduling maintenance once performance falls too low or other warning signs appear.
Since you’ll only schedule maintenance when it’s truly needed, you won’t be wasting your maintenance budget on unneeded work. Additionally, you’ll avoid the significant expenses associated with reactive maintenance, as you’ll get any repairs or replacements resolved before they become larger problems.
Take a look at some of the operations savings identified by Aveva, an industrial software company in the UK.
3.2) Decreased downtime
One of the key benefits of preventative maintenance is that it reduces your unscheduled downtime, which is more disruptive and harder to plan around. But since you’re performing maintenance services according to a fixed schedule, whether they’re needed or not, preventative maintenance significantly increases your scheduled downtime in the process.
Predictive maintenance reduces both scheduled and unscheduled downtime, ensuring your equipment only gets repairs and services when needed.
It’s also worth noting that technicians need less time for maintenance when it’s not an emergency, so compared to reactive maintenance, you’re reducing the duration of most instances of downtime as well.
3.3) Greater asset lifespans
When you take better care of equipment, it lasts longer. Machinery doesn’t work like muscles, where pushing it to the breaking point makes it stronger. Pushing equipment too hard will often cause it to break down sooner in the future. And by letting components fail, you run the risk of causing larger failures, which could force you to replace the entire piece of machinery.
Like preventive maintenance, predictive maintenance extends the life of your equipment by ensuring it receives regular service and minimal wear-and-tear.
3.4) Better inventory management
One of the worst aspects of reactive maintenance is that it’s harder to keep the parts you need on hand—because one failure can easily cause another, and you’re not tracking which parts are approaching their intended lifespan or nearing failure.
While preventive maintenance helps you plan ahead and keep the necessary parts on hand, it also consistently results in wasted parts. You’re replacing components on a fixed schedule, not based on their actual life cycles. Predictive maintenance helps you spot issues early, so you have time to get the parts you need before something breaks.
3.5) Safer work environments
Equipment failures can be extremely dangerous. Depending on the machinery involved and when a breakdown occurs, it can easily cause injury or death. This may result in lawsuits, permanent damage to a business’s brand, compliance penalties, and greater scrutiny from oversight organizations.
Predictive maintenance helps protect workers from using equipment that’s on the brink of failure and detects potential breakdowns before they occur, regardless of whether the equipment is due for service.
4) How cellular IoT is revolutionizing predictive maintenance
Predictive maintenance relies on connectivity. And while ethernet is readily available in many industrial environments like factories and power plants, remote settings often lack the infrastructure needed for these hardwired connections. This forces businesses to either heavily invest in new infrastructure or turn to wireless solutions like cellular IoT. Increasingly, cellular connectivity is proving to be a versatile solution for predictive maintenance and smart manufacturing.
Here are some of the key reasons why.
4.1) Cellular infrastructure is already globally deployed
Mobile Network Operators (MNOs) have been building up cellular network infrastructure for decades. There are cellular towers all over the world, so wherever you deploy, there are already networks available. Using global IoT SIMs like EMnify’s, your devices can connect to more than 540 networks in over 180 countries with a single SIM card, enabling you to scale and expand anywhere in the world, and letting your customers relocate equipment as desired.
You don’t have to build or buy cellular infrastructure—you just connect to it. In remote applications like oil rigs or wind farms, cellular IoT is becoming an increasingly popular solution for predictive maintenance.
4.2) Solutions like EMnify are “air gapped”
A major challenge with predictive maintenance is ensuring that your data doesn’t cross through the public Internet, where it could be intercepted and misused. Every connected device presents a potential risk to your larger network. But with cellular solutions, like EMnify, there’s an “air gap” protecting your data from public networks. Using IPSec, OpenVPN, and Cloud Connect, we create Virtual Private Networks (VPNs) to keep your transmissions private.
4.3) It allows OEMs to embed connectivity in their equipment
Modern Original Equipment Manufacturers (OEMs) often want their equipment to have built-in connectivity capabilities. Using cellular IoT lets OEMs bypass their customers’ IT departments by relying on a secure, independent connectivity solution. Their devices connect right out of the box, and their customers don’t have to wonder if the device poses a security vulnerability to their network.
4.4) Cellular connectivity is highly reliable
Predictive maintenance is often used on mission-critical components, systems, and equipment. You can’t afford to lose visibility into whether this machinery is performing as expected. Cellular networks are designed to deliver continuous service, and with a solution like EMnify, there are several layers of built-in redundancy to ensure you always have the strongest signal possible.
4.5) It requires little to no expertise to implement
Sometimes a barrier to implementing predictive maintenance is a lack of connectivity expertise. Network topology can be complicated, and navigating the various protocols involved in connectivity is overwhelming if it’s not your field. But with EMnify, you don’t have to have in-house experts. You can focus on your application, and we’ll take care of the connectivity.
4.6) You can connect equipment that wasn’t connected before
When machinery wasn’t designed to be connected to a network, it can be difficult to retrofit connectivity later on. But cellular connectivity is easy to implement, whether your equipment was originally built for it or not.
5) Connect your predictive maintenance solution with EMnify
EMnify is a leader in cellular IoT connectivity. Thousands of businesses use our global IoT SIMs to keep their devices connected all over the world. Whether you’re an IoT veteran or you’ve never built a connected device before, getting set up with EMnify is easy. With our multi-layered approach to network security, we keep your data and devices secure—so your customers see your devices as assets, not liabilities.
Cellular connectivity is ideal for predictive maintenance solutions that need to deploy in remote areas or operate independently of a customer’s private network. Not sure if cellular is the right IoT connectivity solution for your business?
Talk to one of our experts. Or sign up for our free test SIMs, and explore our tech for yourself.
Get in touch with our IoT experts
Discover how emnify can help you grow your business and talk to one of our IoT consultants today!
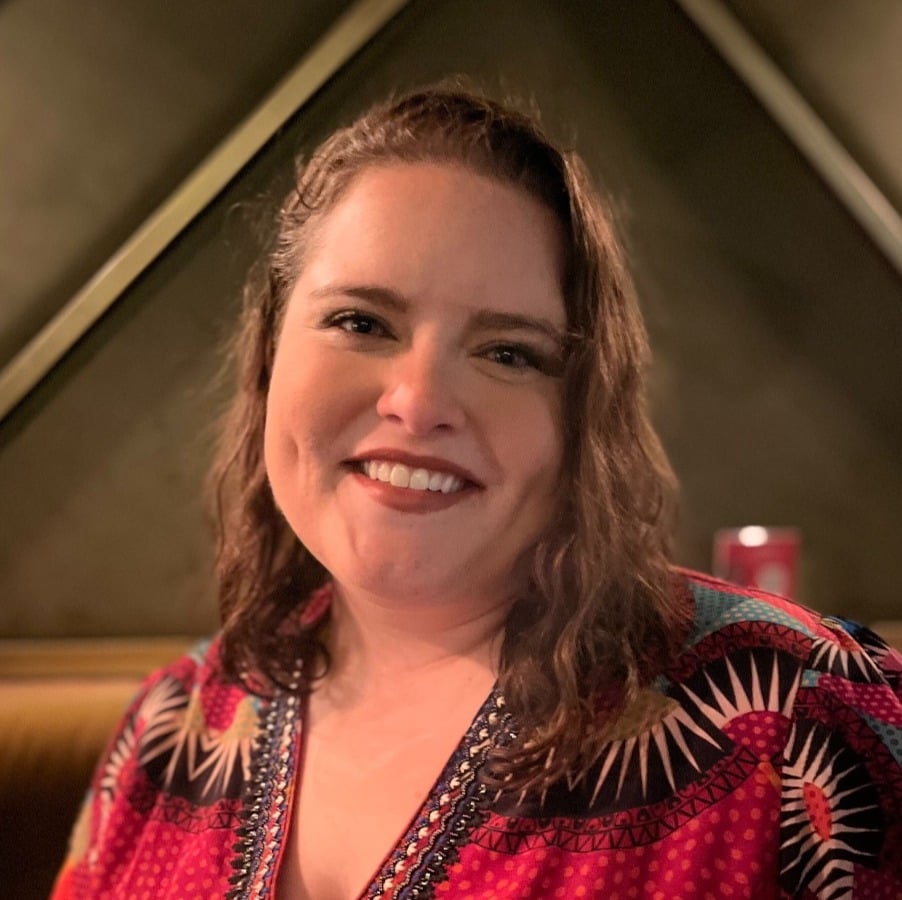
Shannon McCrocklin
Shannon has over seven years of experience communicating with audiences on behalf of businesses. She is passionate about making complex, technical topics easy to understand for readers of all backgrounds.