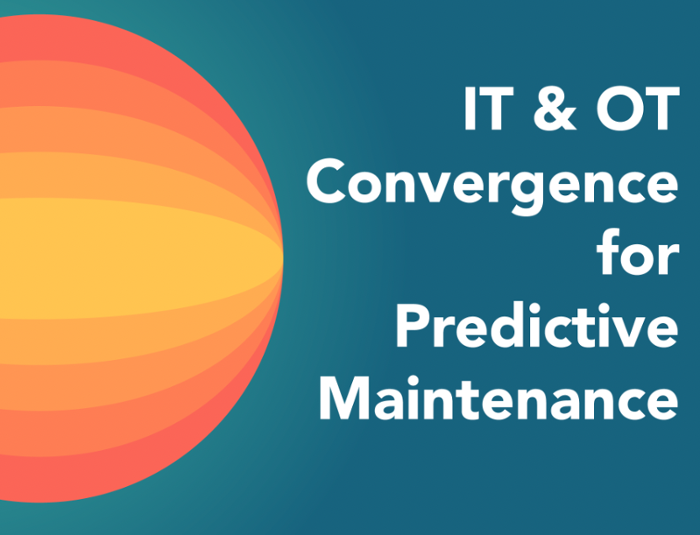
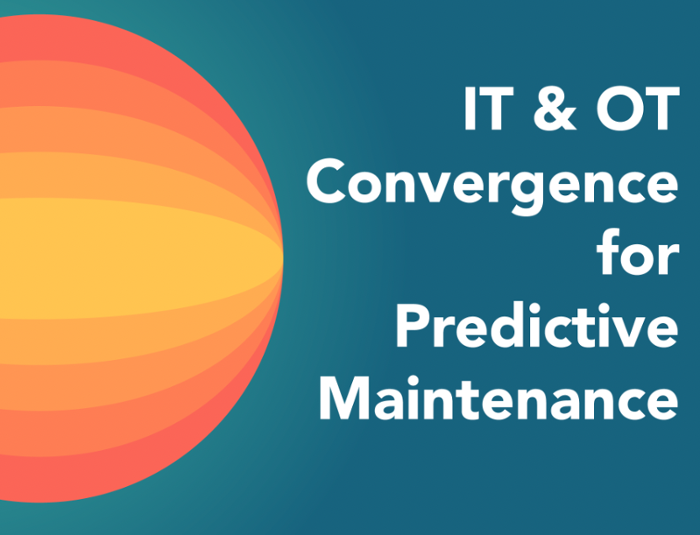
When machine manufacturers or system integrators are building a predictive maintenance or IoT application for smart factories, the question inevitably comes up: how will you get buy-in from IT and OT to send factory data to your cloud application?
To successfully sell your machine or integrated predictive maintenance application to manufacturers, you must first overcome various connectivity objections and strict requirements from IT and OT departments. IT and OT departments have drastically different perspectives on how to approach and even evaluate machine connectivity and it is very difficult to make both teams happy. In this blog, we will discuss key considerations to get IT managers and operations managers on the same page when it comes to IoT connectivity for predictive maintenance.
The IT Perspective on Connectivity
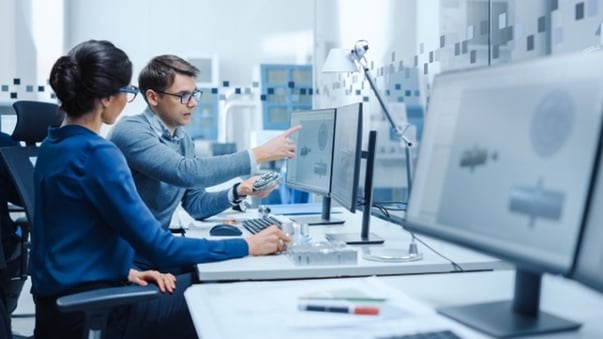
For IT Managers, network security, ease of use, and integrations are top of mind for new smart machines connected to factory networks. However, predictive maintenance applications are built on the cloud and must receive data through the public Internet – presenting cybersecurity concerns to IT.
1. Network Security
The first challenge you face when deploying machines for predictive maintenance is the need for mission critical reliability, and this translates into requiring machines to maintain their connections to factory networks 24/7, 365 days a year. Unplanned network downtime is often caused by unreliable network connectivity due to a lack of network redundancy, poor network connections in remote areas, and consumer-grade networking equipment.
Unreliable connectivity leads to lost productivity and when machines are not producing output, manufacturers have additional costs associated with sending repair technicians on costly trips to troubleshoot machines in person.
2. Ease of Use
Once a machine is enabled for predictive maintenance, the job doesn’t stop there. IT and OT must collaborate to maintain the machine and maximize the uptime. Machines with complex network configurations require in-depth networking knowledge to operate. They also consume a large amount of IT resources to maintain. So IT managers prefer connectivity that is easy to deploy in their existing network and doesn’t require a lot of hand holding from IT to maintain or troubleshoot. Centralized network management software and audit logs also help with system monitoring and troubleshooting to ensure machine operators can resolve network issues on their own with less IT support.
3. Integrations
A third consideration for IT is how well a new technology integrates with or plugs into the existing IT technology stack. This is important for the day-to-day IT managers because it enables them to send data to their existing cloud infrastructure in minutes instead of weeks by avoiding the need to build custom integrations. Some cellular IoT platforms like emnify even integrate with cloud service provider and ERP system, enabling IT to seamlessly transfer data between existing systems and their business applications. APIs can also accelerate the development of custom web applications that need machine connectivity data to display on dashboards for upper management to have central visibility of IT assets.
Now let’s explore what connectivity considerations are top of mind for operations technology professionals and possible sources of friction with IT.
The OT Perspective on Connectivity
For OT managers, network reliability is more important than network security because factory performance is judged by production quantity and quality. A machine's ease of use is important to reduce the time required to train and onboard staff. And central network visibility is an essential feature to empower factory operators with the ability to quickly identify and resolve connectivity issues.
1. Network Reliability
Industrial machines are made for 24/7, 365 days per year operations and industrial engineers expect connectivity to have the same level of mission critical reliability. So operations engineers require connectivity solutions that have network redundancy and low latency. Redundancy is key for network reliability so that when a primary network connection goes down, there is a backup network connection to prevent costly downtime from unreliable factory networks. Low latency networks provide more up to date and accurate information during factory operations for monitoring machine performance. Cellular technology provides reliable and low latency connectivity regardless of the network infrastructure on a factory premise.
2. Ease of Use
Let’s face it. Operations engineers are experts at factory automation, but not at network engineering. Consequently, any networking technology used for factory operations needs to be easy to use and operable through an intuitive graphical user interface. Better yet, if you leverage a cellular IoT platform with REST APIs, you can automate the setup and configuration of groups of devices at a time – saving precious OT and IT resources when deploying machines. As a result, user-friendly connectivity platforms reduce the friction between OT and IT.
3. Central Network Visibility
SCADA and MES systems provide crucial visibility into factory operations and machine performance. A predictive maintenance cloud application must provide factory operators with the same level of visibility into network traffic and performance. The ability to remotely troubleshoot and monitor machines empower operations engineers with the ability to visualize network usage, identify critical events like network outages, and prevent machine failure.
As you can see, IT and OT managers often have different priorities – and these differences often lead to friction when deploying new machines for predictive maintenance. Let’s discuss those points of friction and how to overcome them with cellular IoT technology.
IT and OT: why can't we be friends?
To understand how to deploy a machine with predictive maintenance that will please the security conscious IT manager and the reliability focused operations engineer, we can start with the two most common scenarios where IT butts heads with OT.
Scenario 1: Data Communication Over Public Internet
For the sake of keeping devices secure, factories today separate their factory networks from the public Internet—which is a technique often referred to as “air-gapping”. When plant managers introduce a new networked connection on their factory network, such as a new machine ready for predictive maintenance, IT must ensure the machine is following the proper security protocols so that the company is not exposed to cybersecurity vulnerabilities.
IT often has to approve new networked connections and OT often feels frustrated by the hoops they have to jump through to comply with IT security policies – abandoning a predictive maintenance enabled machine deployment altogether if the barriers to approving a machine’s security features are too high. But data needs to travel through the public Internet in order to go to the cloud for machine learning and predictive maintenance to take effect.
How can you accomplish this data communication from a factory device to the cloud securely? This is where VPN and IPsec technology come to the rescue. These technologies enable factories to send data securely from a machine to the cloud with data encryption.
For example, IPSec technology can encrypt data communication between a cellular provider and a customer’s cloud-based predictive maintenance application.
Scenario 2: The Security Versus Productivity Tradeoff
Operations are under pressure to maximize productivity and have strict output targets. Unlike enterprise devices like corporate PCs, which are frequently updated with security patches that incur minimal inconveniences to enterprise users, factory equipment downtime for security updates can costs tens of thousands or even millions of dollars in lost productivity. This leads to friction between IT who wants the most secure, up-to-date networked equipment and OT who has more of a mentality, “If it ain’t broke, why fix it?”
So how do we resolve this source of friction? The answer is simple – adopt networking technology like a cellular IoT platform that has network security capabilities like VPN or IPsec and industrial-grade reliability. This way your predictive maintenance enabled machine can operate reliably for mission-critical applications and securely by complying with IT security policies.
In summary, we recommend adopting a cellular IoT platform
IT and OT can be friends and partners in deploying predictive maintenance applications and machines if they leverage the right technology. Our recommendation is to adopt a cellular IoT platform like emnify for predictive maintenance applications because it can help IT and OT managers overcome the tradeoff between security and reliability by having the best of both worlds:
- A secure cellular IoT network that sends encrypted machine data to a cloud application with API integrations and reduces the need for IT support.
- A reliable, user-friendly cellular IoT platform with industrial-grade reliability and central network visibility to enable factory operators to resolve connectivity issues faster.
Benefits of a Cellular IoT Platform
About emnify
From reliable connectivity and secure remote access to machines to powerful APIs, automated cloud integration and advanced security features, emnify provides you with all the tools you need to deploy and operate your smart machines for predictive maintenance anywhere and at any scale.
Learn more about how we can help your predictive maintenance application here or contact our cellular IoT expert to book a free consultation today.
Get in touch with our IoT experts
Discover how emnify can help you grow your business and talk to one of our IoT consultants today!
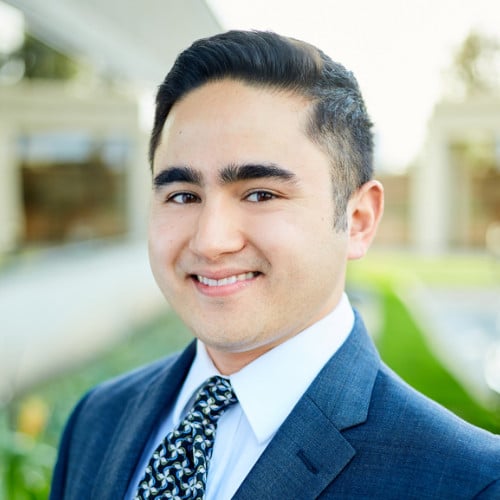
Nathan Schlaffer
More than 7 years of experience translating hi-tech connectivity and SaaS products for Internet of Things into simple and compelling use cases across a broad range of vertical markets from manufacturing to transportation to oil and gas.